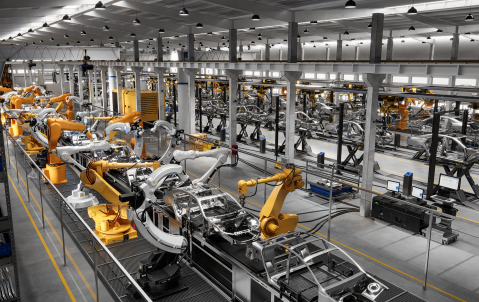
Why are product recall incidents on the rise?
Post-pandemic challenges and economic factors test manufacturers but also challenge insurers not to let an overflow of capital and competition distort the true price of risk and threaten the long-term sustainability of product recall insurance
Product recall insurance claims are on the rise, both in terms of frequency and severity. According to Sedgwick’s Recall Index 2022 Edition 1, the first quarter of 2022 alone saw 913.8 million units recalled across the five market sectors of automotive, pharmaceutical, food and beverage, medical devices and consumer products, compared to a total of one billion for the whole of 2021, and representing the highest total number of units recalled in a single quarter for the past decade.
“Many of the problems stem from challenges arising from the pandemic coming to light in the last twelve months,” says David Burke – Product Recall Line Underwriter for Hiscox London Market.
Why? “Many of the problems stem from challenges arising from the pandemic coming to light in the last twelve months,” says David Burke – Product Recall Line Underwriter for Hiscox London Market. “Take the food manufacturing industry, for example, where some manufacturers prioritised the supply of food to make sure they could keep products on the shelves, meaning the required food safety and supplier audits may not have happened.”
There are also other factors at play like staff shortages, ongoing supply chain challenges, inflation and cost control, and transport issues; all of which are continuing to affect not just food manufacturing but also other sectors such as the automotive industry from a product recall perspective. Surprisingly, Burke adds, despite the recall losses: “The insurance sector still has plentiful capacity for product recall risks, reflecting the number of new entrants and the appetite to write new business despite the deteriorating claims picture.”
Pandemic fallout
The fallout from the pandemic is likely to continue impacting the product recall market for at least the next 12-24 months, says Burke, who points to not just errors by food manufacturers but also a lack of oversight by regulators over the pandemic period. “Issues would have been picked up by regulators through their usual audits of factories, products, and supply chains, but these just didn’t happen.” And those issues would have been more likely as manufacturers worked at full stretch to keep the supply chain moving, leading to inevitable problems with food safety. As the supply chain became more fragmented, adds Burke, manufacturers would have been sourcing new ingredients from new suppliers sometimes because they can’t get an ingredient from an old supplier, or sometimes because they need to save money given there is only so much cost they can pass on to consumers. If the buyer doesn’t keep to their original supplier approval procedures, says Burke, particularly given the rise of counterfeit products, then it can lead to potential product recall problems. “We are also finding that some companies are now reliant on a single supplier whether that be for raw ingredients or as a co-manufacturer. As a result, when a loss occurs the business is shut down with no alternatives. The manufacturer who has multiple – or at least two – supply options is able to pivot and mitigate, and in many cases stop the business interruption loss from occurring.”
“We are also finding that some companies are now reliant on a single supplier whether that be for raw ingredients or as a co-manufacturer. As a result, when a loss occurs the business is shut down with no alternatives. The manufacturer who has multiple – or at least two – supply options is able to pivot and mitigate, and in many cases stop the business interruption loss from occurring.”
In addition, there have been workforce problems says Burke: “Food manufacturers can’t get the experienced staff they need for what is often a very tough job, which means utilising contract and temporary workers who might not know the factory procedures resulting in problems that can lead to recalls.” In the US, Burke adds, staff cuts in relation to the pandemic – where ‘at-will’ employees generally get only two weeks’ severance pay making it a quick way to save money by getting rid of higher paid employees – has seen production line employees keeping their jobs and higher priced staff/supervisors let go which, again, has impacted quality issues.
Other issues include transportation challenges and the ability to keep temperatures at the right level; high energy costs meaning some manufacturers could be changing their processes in cooking and freezing to reduce energy usage which could cause contamination issues; and environmental issues as global warming causes problems from water safety, to heat stress in livestock, and increasing ambient storage temperatures eroding the shelf life of products. “It feels like manufacturers are up against so many headwinds,” says Burke. “We’ve seen this in product recall claims not just in food and drink, but also in other sectors such as automotive component manufacturers who are increasingly exposed to uncertain supply chain issues. The just in time manufacturing process is not working.”
Squeezed margins
In turn, adds Andy Kyle, Product Recall Underwriter for Hiscox London Market, these operational pressures are also causing more commercial concerns. “As margins are squeezed, manufacturers are taking the opportunity under their contracts to squeeze their suppliers if they have caused any issue around contamination, defect, or any other kind of inconvenience. The demands for money being passed from the top of the supply chain downwards are becoming larger. And while some companies take it on their balance sheet, increasingly they look to product recall insurance as the backstop.”
“As margins are squeezed, manufacturers are taking the opportunity under their contracts to squeeze their suppliers if they have caused any issue around contamination, defect, or any other kind of inconvenience. The demands for money being passed from the top of the supply chain downwards are becoming larger. And while some companies take it on their balance sheet, increasingly they look to product recall insurance as the backstop.” adds Andy Kyle, Product Recall Underwriter for Hiscox London Market.
Loss ratios deteriorate
As a consequence of all these factors, says Burke: “The insurance industry is paying out more on product recall claims, loss ratios are worsening and the worry is that this situation continues which means we must take underwriting measures. If a business can prove their supply chain procedures are still robust even if they are using different suppliers, for example, we will see that as a good risk. We are looking at all these new risk exposures and calculating how our current and potential customers are exposed to them and then underwriting accordingly.”
Product recall market lacks discipline
The challenge for the product recall insurance market, Burke says, is that while the risk exposure has never been worse, there has never been so much capacity and new markets coming in to offer the product. “While prices should be increasing for this product, they are going down in many instances due to Insurer competition. I’ve been in this class of business for 35 years and never found it this tough with the claims environment so challenging, combined with the markets being so competitive regarding terms and conditions, wording, pricing and a lack of underwriting discipline.”
Doubling down on risk selection
What shape, continues Burke, will the product recall market be in if it continues to lack that discipline? “Markets pull out of product recall as quickly as they enter, so will we see a boom and bust for buyers? Insurers need to make an underwriting profit over a cycle to show shareholders it is a viable product and can produce a return on capital. The worry is that profit dynamic is on the verge of being broken for many.”
With the economic and post pandemic challenges unlikely to settle down in the short term, Hiscox will “double down” on risk selection to make sure product recall remains viable to help businesses through the next year of volatility and uncertainty says Burke: “We will continue to support those customers who can show they are managing their recall risk and have a well-developed approach to areas like crisis management and business continuity planning. Ultimately, it’s our job to be here to offer a viable product for our customers and make sure they get the protection they need to navigate through the tough times.”